For steel producers, roller hearth furnaces are essential for altering the properties of the goods passed through the furnace, whether bars, tubes, plates, or wire coils. Regardless of the furnace size or temperature, which can vary greatly, having a controlled, uniform heat is crucial for the quality of the final product.
Processes for roller hearth furnaces in short
A roller hearth furnace can be used for several heat treatment processes to alter the properties of the goods that pass through the furnaces. Examples are annealing after a cold-forming operation, slab reheating, stress relieving, hardening, normalizing, and tempering. Another area of use is to preheat blanks for a subsequent hot-forming operation such as hot stamping. The roller hearth furnace works equally well for different goods, including bars, tubes, plates, and wire coils.
Jonas Ekström, Application Specialist, Business Development Steel, Kanthal.“These furnaces typically operate continuously 24/7 so the more stable the process is, the better,” says Jonas Ekström, Application Specialist, Business Development Steel, Kanthal. “If the material is heated unevenly or the temperature inside the furnace fluctuates, it becomes much harder to get the desired properties and quality in the finished steel.”
Multiple cost savings deliver fast return in investment
When you factor in the energy efficiency gains and the corresponding reduction in CO2 emissions, the business case for electric heating becomes stronger.
The conventional heating solution for rolling hearth furnaces is gas heaters, but the industry is increasingly moving toward electric heating because of the many benefits. For one, thermal efficiency is far higher at almost 100 percent, meaning that virtually all the heat produced is used inside the furnace. On the other hand, gas heaters typically have thermal efficiency at around 30 to 40 percent since so much heat is lost in the exhaust.
Historically, producers have chosen gas over electric options as it has often been cheaper. However, rising gas prices and increasing carbon taxes mean this is changing. When you factor in the energy efficiency gains and the corresponding reduction in CO2 emissions, the business case for electric heating becomes stronger.
“Not only can you reduce costs through lower energy consumption, but you can also reduce costs from carbon pricing initiatives or avoid possible penalties for emissions,” Ekström says.
In addition, the temperature accuracy from electric heating is far more precise and controllable, which can help increase production yields. “With a gas heater, you will always have a hotspot where the burner is located, and the center of the flame can be close to 2,000°C (3,630°F). In contrast, an electric heater radiates an even temperature across the whole element, improving steel’s quality.”
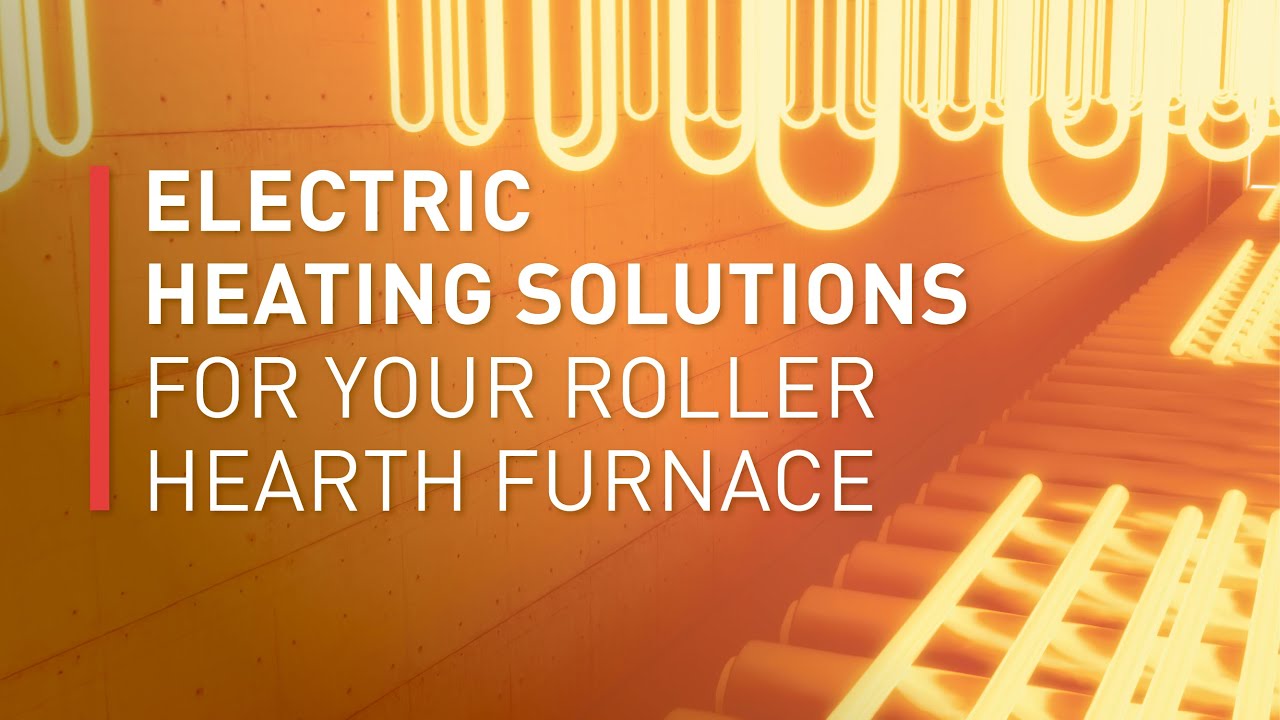
Vast experience and a broad portfolio
With decades of experience working with electric heating, Kanthal has developed solutions suitable for roller hearth furnaces, depending on the furnace’s size, design, and requirements. For temperatures of up to 1,250°C (2,280°F), the most common solutions are Tubothal® metallic heating elements in combination with Kanthal® APM, APMT, Kanthal® AF or NiCr tubes, or Fibrothal® prefabricated heating modules for temperatures up to 1,350°C (2,450°F). For temperatures up to 1,850°C (3,360°F), there are Globar® silicon carbide (SiC) heating elements or Kanthal® Super MoSi2 heating elements.
“The main questions we often get from customers are based on concerns about electric heating’s ability to deliver enough power and high enough temperatures,” Ekström says. “But as we have proven for many years, the power output is on par with gas, and then you get all these other benefits too. If you’re still using gas heaters to heat the inside of tubes, you should swap them for electric as soon as possible.”
Four benefits to using electric heating in roller hearth furnaces
- Improved energy efficiency: While 60 to 70 percent of the heat generated by a gas heater will be lost in the exhaust, virtually no heat is lost with an electric heater, which increases thermal efficiency to almost 100 percent and reduces energy costs significantly.
- Zero CO2 emissions: The process effectively becomes emissions-free, if the electric heater is powered by renewable energy.
- Precise temperature control: Compared with a flame, an electric heater can be controlled to deliver an exact temperature.
- Excellent uniformity: As there are no hot zones, electric heaters deliver an even, uniform temperature across the whole element.
相关产品
Kanthal产品和服务系列
Read more
Electrification made easy