Within steel manufacturing, the annealing process is one of the most critical when it comes to the quality of the final product. The temperature range in the annealing furnace can vary greatly depending on the desired outcome, from room temperature right up to near the melting point, but in almost all cases reaching a precise temperature is essential.
Annealing process in short
The annealing process involves heating the carbon steel or stainless steel to a specified temperature for a set period, before allowing it to cool in a controlled manner. The purpose is to change the mechanical and chemical properties of the finished steel, such as its ductility and hardness. The temperature and duration will vary greatly depending on the desired outcome.
Onintze Achutegui, Technical Marketing Manager EMEA, Kanthal.“This is where you set the steel’s mechanical properties such as its strength and hardness,” says Onintze Achutegui, Technical Marketing Manager EMEA at Kanthal. “It’s important to control the process, because sometimes the required temperature can be specific, and the window for achieving it can be quite tight.”
An emissions-free annealing process
Electric heating can completely decarbonize the annealing process if the electricity derives from a renewable source.
While many steel producers use gas heaters in their annealing furnaces, this is becoming increasingly problematic due to the need to move away from fossil fuels. By contrast, electric heating has the potential to completely decarbonize the annealing process if the electricity derives from a renewable source.
Compared with gas, electricity emits no harmful emissions or exhaust gases into the factory and this, combined with lower noise, greatly improves the working environment.
In addition, electric heating can provide far greater temperature control, one of the most important functions of the annealing furnace. “Because it is not using an open flame, it’s possible to achieve very tight temperature tolerance in a controlled continuous mode,” Achutegui says. “It does not need to be continuously monitored and adjusted – it can just be left to run. And it is also very energy efficient since almost all the heat produced is used in the furnace.”
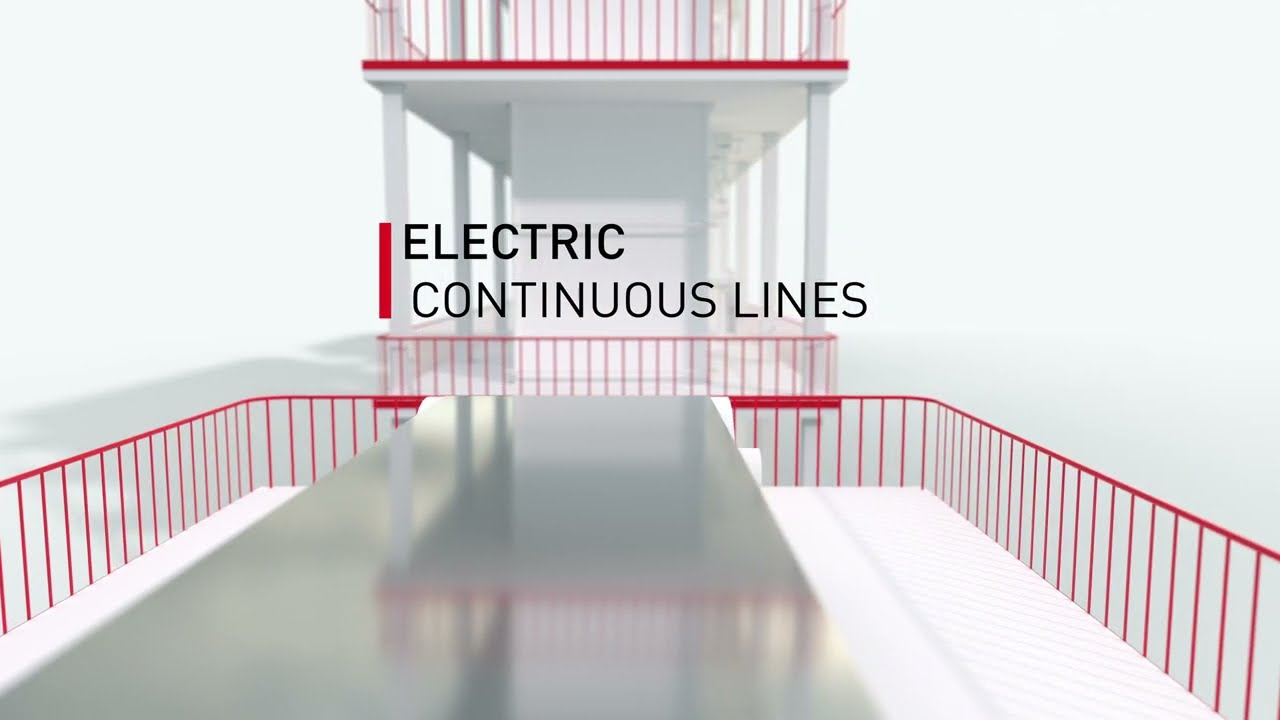
A broad portfolio for meeting all furnace needs
The beauty of Kanthal’s portfolio is its flexibility. It includes everything from single elements to integrated systems.
With decades of experience working with industrial heating solutions, Kanthal has developed a broad range of materials suitable for annealing furnaces, depending on the temperature requirements and atmospheric conditions. Its Tubothal® metallic cartridge elements can work for temperatures up to 1,250°C (2,280°F). For higher temperatures up to 1,625°C (2,927°F) it can offer its Globar® silicon carbide (SiC) heating elements, and for temperatures up to 1,850°C (3,360°F), it has its Kanthal® Super MoSi2 heating elements. Kanthal can also customize its products and designs to suit specific requirements.
“There is no standard for building an annealing furnace – it’s very much process-driven,” Achutegui says. “But the beauty of Kanthal’s portfolio is its flexibility. It includes everything from single elements to integrated systems. Sometimes you need different types of solutions for the same furnace, for example, different gradients or speeds, and our portfolio is broad enough and flexible enough to accommodate that. We can develop a solution.”
Four benefits to using electric heating in annealing furnaces
- A cleaner, quieter working environment: Electric heaters do not emit harmful exhaust gases in the factory, and the noise levels are far lower.
- Zero CO2 emissions: The process effectively becomes emissions-free, if the electric heater is powered by renewable energy.
- Precise temperature control: Compared with gas, an electric heater can be controlled to deliver a precise and consistent temperature.
- Increased thermal efficiency: As virtually all the heat produced is used inside the furnace, and not released with exhaust gases, thermal efficiency is typically over 90 percent.
相关产品
Kanthal产品和服务系列
Read more
Electrification made easy